Extending crane wire rope replacement intervals to defer OPEX
Client: International offshore drilling contractor
Industry: Drilling
Asset: Drillship
Location: Cyprus
Year: 2021
Challenge
Wire ropes are one of the hardest working components of cranes. Despite suffering all manner of weather and working conditions, they continue lifting, thanks to their incredible design. However, even wire ropes have limits and continued fatigue and strain will eventually manifest as material defects, which reduce strength and increase the chances of critical failure.
As such, some crane owners implement time-based replacement intervals. However, in cases where intervals are too short given the operating history, third-party assurance is needed to verify that the wires are in good condition and can remain in service.
In this particular scenario, the client’s policy is to replace ropes every two years. With the costs, Health, Safety and Environment (HSE) risks and time associated with wire rope replacements, they turned to Axess Middle East for a solution to retain the existing ropes in service.
Solution
Axess Middle East was subsequently contracted to perform condition-based inspection and maintenance on all major cranes on its drillship, including four lattice boom deck cranes and three gantry-type subsea cranes.
The personnel inspected the ropes using electromagnetic (eMAG) technology, otherwise known as Magnetic Rope Testing (MRT). The technology uses the principles of Magnetic Flux Leakage (MFL) to determine material discontinuities including corrosion, broken wires, and defects like bird caging. It is far more powerful than the human eye, allowing users to “see” inside the rope to the critical core strands.
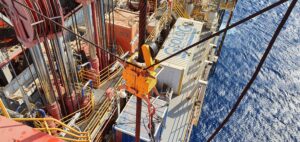
As the Project Manager of this project, Rod Matzdorff, Operations Manager of Axess Middle East, said, “Performing eMAG inspection of wire ropes in-situ provides quantitative data and helps to accurately determine the actual condition of the ropes. This leads to potential life extension, and in turn, defers replacement costs as the replacement intervals are extended.”
After identifying the ropes that were compliant for service life extension, a maintenance program was carried out to replace the “lifeblood” of the ropes – grease.
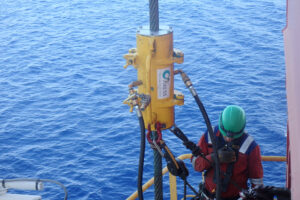
Grease oxidises over time, drying out and loses its lubricity. Using pneumatic power-driven machinery, Axess mechanically removed old grease, and injected high-specification new grease into the rope core and strands – something only a purpose-built machine is capable of.
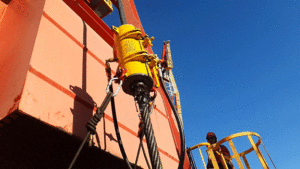
Results
With the ropes thoroughly inspected and freshly greased, the client gained the confidence and peace of mind to keep them in service, therefore, deferring OPEX and improving efficiency.
But the benefits went beyond this – huge cost savings was achieved since the same personnel also carried out multiple scopes while onboard, including annual crane inspection, DROPS surveys, general Non-Destructive Testing (NDT), as part of the larger re-activation campaign.
Due to dynamic project planning, Axess was able to reduce mobilisations, Personnel on Board (POB), therefore, achieving monetary savings and a reduction in carbon emissions.
If you are interested in eMAG inspection and lubrication for your wire ropes, please reach out to us. Reference will be provided upon request.