Safe and cost-effective flare tip replacement on offshore platforms
Client: Large Oil & Gas producer in the Middle East
Industry: Oil & Gas
Assets: 4 fixed platforms
Location: Offshore Qatar
Year: 2020/21
Challenge
Flare systems are an integral part of the safety systems on oil and gas-producing assets. They facilitate the controlled disposal of hydrocarbon-containing material.
Due to operational wear and tear, the flare tips (typically weighing 1 to 4 ton) of four fixed platforms were scheduled to be replaced in two shutdown campaigns.
The client had contracted Axess Group to replace the flare tips consecutively, within a short time frame. It was important for the replacements to be completed as soon as possible since a longer shutdown period would mean a more significant loss in revenue for the client.
As flare tips are located at height, above deck or sea, and out of reach of the assets’ deck cranes, flare tip replacements are complex operations that need to be well-planned to ensure safety and reliability.
Solution
As the production shutdown window was narrow, we decided on the helicopter method together with the client.
“At Axess, we have extensive experience in both helicopter and mechanical methods for replacement of flare tips. We understand that every project can have its constraints, thus, we always make sure to thoroughly assess the situation and advise on a solution that best suits our client,” said Bjørnar Bøe Lundberg, Team Leader at Axess Group.
Typically, prior to such a project execution, Axess will mobilise an experienced Field Engineer to conduct a site survey to assess the details of the site. However, an alternative measure was required due to the COVID-19 pandemic. Instead of a site survey, Axess guided the client’s offshore personnel to collect the required data as part of an extensive desktop study.

The replacement process on each of the four platforms was the same. The team first rigged and prepared the old and new flare tips for lifting. Subsequently, they used a helicopter to lift the old flare tip from the riser and positioned it on the laydown area of the helideck. Finally, the new flare tip was picked up from the platform laydown area and transferred to the flare tip platform for installation.
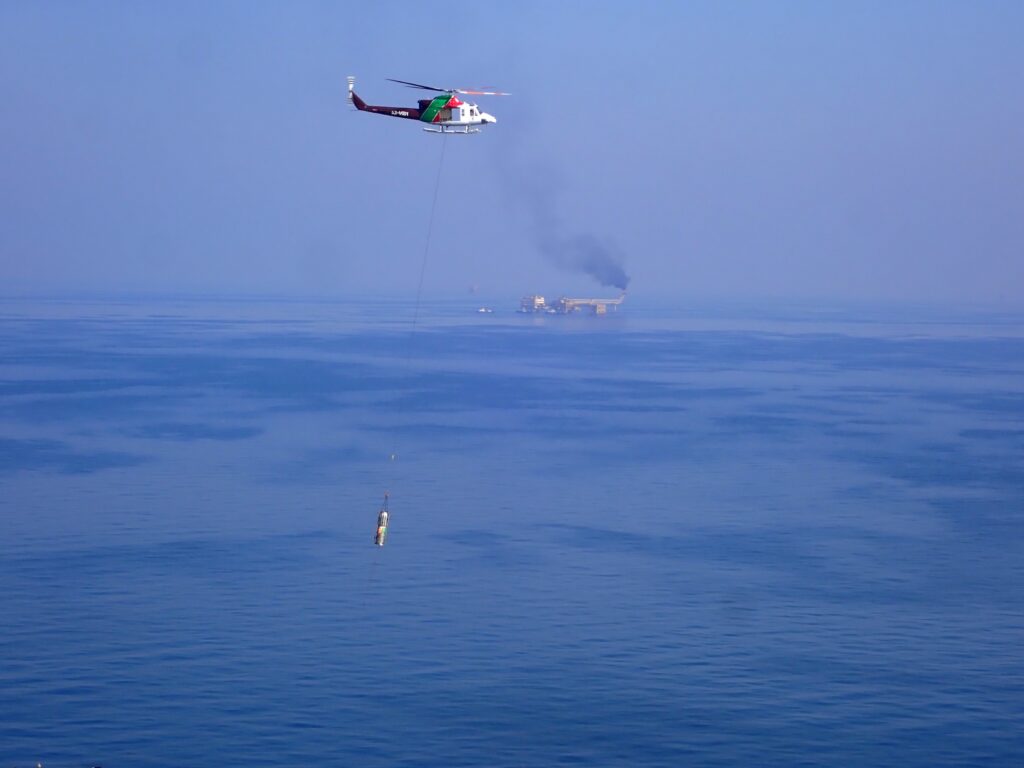
Results
Due to excellent preparation, communication and teamwork, the team successfully replaced all four flare tips safely, within time and budget.
“Our global network of engineering experts enables us to provide a wide range of quality services to offshore assets located anywhere in the world. We are delighted to have helped another client with flare tip replacements,” Bjørnar added.
The client’s Campaign & Shutdown Lead said: “Another flare tip replacement completed during this pandemic with all the constraints that we are familiar with. Thanks to the team for the excellent work done.”
If you are interested in flare tip replacement for your offshore assets, please reach out to us.